Material modelling

Material models / sub-routines
A reliable structural analysis requires precise tools. Not only the software environment but above all the integrated material models have a significant influence on the quality of the results of a simulation. With the standard models, especially inhomogeneous materials can only be described inadequately. his includes metals with specific forming direction, foamed plastics, 3D printed parts and, of course, composites.
We use numerous specific material models that exceed the possibilities of the standard descriptions. All necessary parameters are formulated as a function of the strain rate and temperature. An adaptation for your specific problems is possible at any time.
- Orthotropic elastic / plastic material models for metals, foamed plastics, homogenized hybrid materials, 3D printed parts with internal heterogeneity as well as thermoplastic and thermoset composites
- Consideration of temperature and strain rate dependence
- Asymmetrical strengths with adapted failure concepts
- Failure mode-related degradation for composites
- Implementation via subroutines for Simulia / Abaqus Standard and Explicit
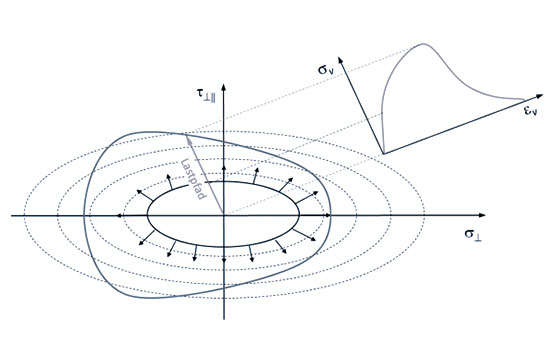
FAILURE BODY
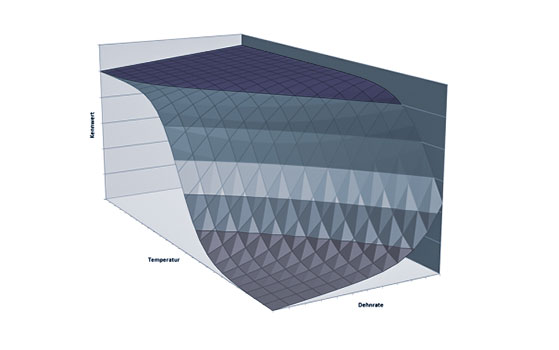
S/N SURFACE
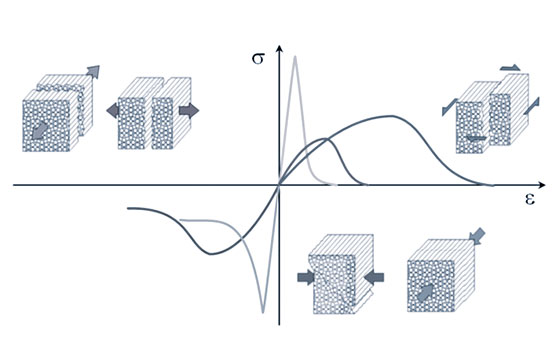
ANISOTROPIC MATERIAL BEHAVIOUR
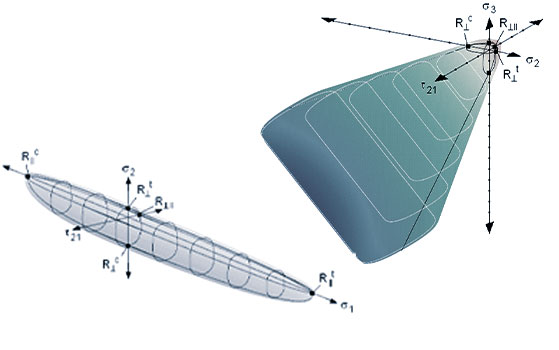
ADOPTED FAILURE CRITERION FOR COMPOSITES
Virtual testing
A deep understanding of the material and its behaviour forms the basis for optimization potential. Where an experimental test only shows an overall result for complex mechanisms, our virtual testing can often provide a much deeper insight.
We visualize the chronological sequence of damage-relevant events from micro to macro scale. These results are the basis for the development of specific material models and adopted failure criteria on the one hand and provide a deeper understanding of inhomogeneity effects like holes or fiber undulation on the other hand.
- Multi-scale virtual testing for a deeper understanding of materials
- Evaluation of the influence of imperfections (e.g. holes or undulation)
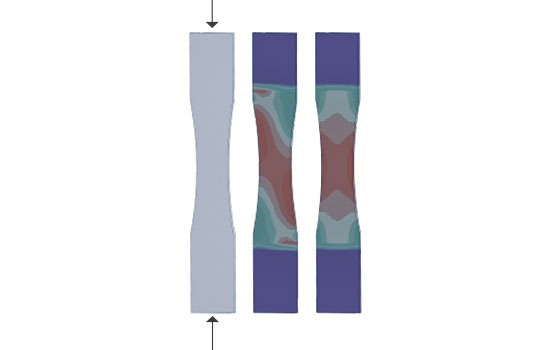
TEST SPECIMEN, MACRO SCALE

MATERIAL BEHAVIOUR ON MESO SCALE
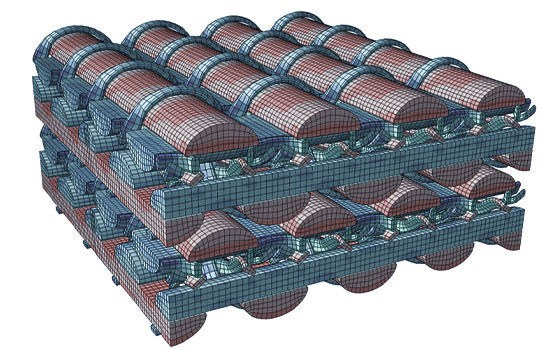
MATERIAL BEHAVIOUR ON MICRO SCALE
VIDEO IOSIPESCU VERSUCH
Material Cards
Our virtual tests provide information on the general material behaviour. The material models allow a mathematical description of this behaviour. For the structural simulation of components, these material models now have to be fed with specific parameters. The basis is provided by data from specimen tests.
In contrast to the classic procedure, in this case only a few „support points“ have to be examined by specimen tests. These are sufficient to calibrate the prepared material models. At this point at the latest, the apparently complex chain of virtual tests and material modelling pays off.
- Calibration of material cards based on a few selected specimen tests
- Upon request, the material models and material cards can be transferred to the customer’s FE environment